The name Jägermeister is known the world over. The namesake company, Mast-Jägermeister SE, has established a strong international reputation with its herbal liqueur and equally recognizable brand. On the one hand, it’s got the iconic logo featuring a stag with a radiant cross between its antlers. And on the other, the distinctive green bottle, whose flattened rectangular silhouette is unmistakably Jägermeister. It’s a look that Jägermeister uses consistently across its entire product line – in all sizes from the large, 1.75-liter and even 3-liter bottles to the standard 0.5 and 0.7 liters right through to the 20-milliliter “mini meister”.
The company has built its filling operations on Krones technology for decades now. Both bottling plants, in Wolfenbüttel-Linden and in Kamenz, are equipped with Krones kit. Among the longest-running machinery is Line 4, which has been in operation since 1993. Although it has continued to provide dependable service, Jägermeister decided in 2023 that it was time for an update. As Bettina Riemenschneider-Schilling, Senior Director Filling Centers at Jägermeister, explains: “We want to keep up with technological advancements, and so it was time for an upgrade.”
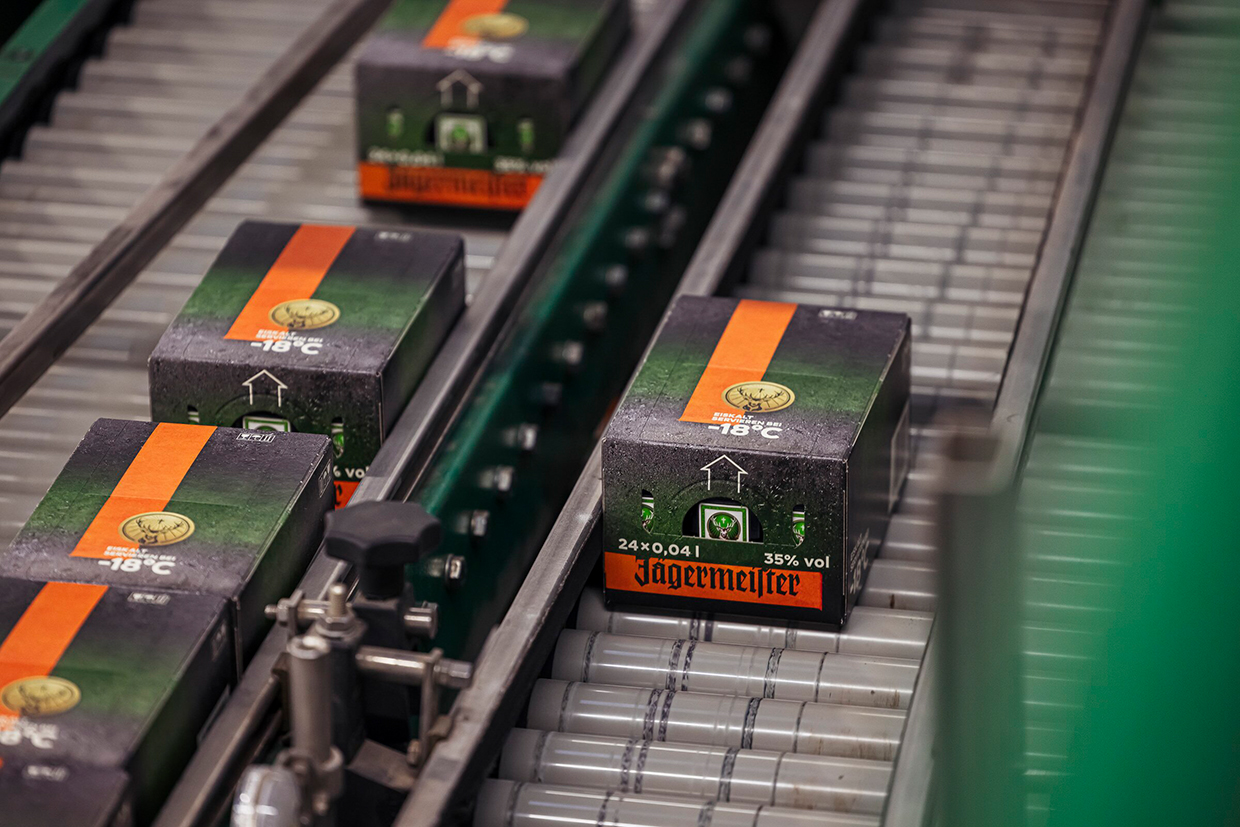
Mast-Jägermeister SE