The well-proven block solution for PET bottle production
Bringing together what belongs together
Blow moulder and filler are an effective team. And that is the reason why we have perfected the popular combination of both machines even further in a single block. With a seamless drive concept, finely tuned transfer interfaces for every production program and precisely operating processes in stop situations, you can count on getting the very best out of your PET bottle line.
At a glance
- Functions: Stretch blow moulding, filling and capping
- Output: Up to 100,000 containers per hour*
- Processing range:
- Non-carbonated and carbonated beverages, soft drinks, cooking oil, beer, wine and ketchup
- Container volume up to 3.5 litres
- Standard and lightweight containers
- Round, square and rectangular containers
- Containers of up to 100 percent rPET
- Hot-filling and cold-filling possible
- Flat caps and sports caps
*depending on the processing range
Beverage containers made from rPET

Material properties, processability, food grade quality: you can find all kinds of interesting facts about the use of recycled PET in our free white paper.
You can be curious: The fourth generation of the Contiform is already in the starting blocks.
Functions and structure
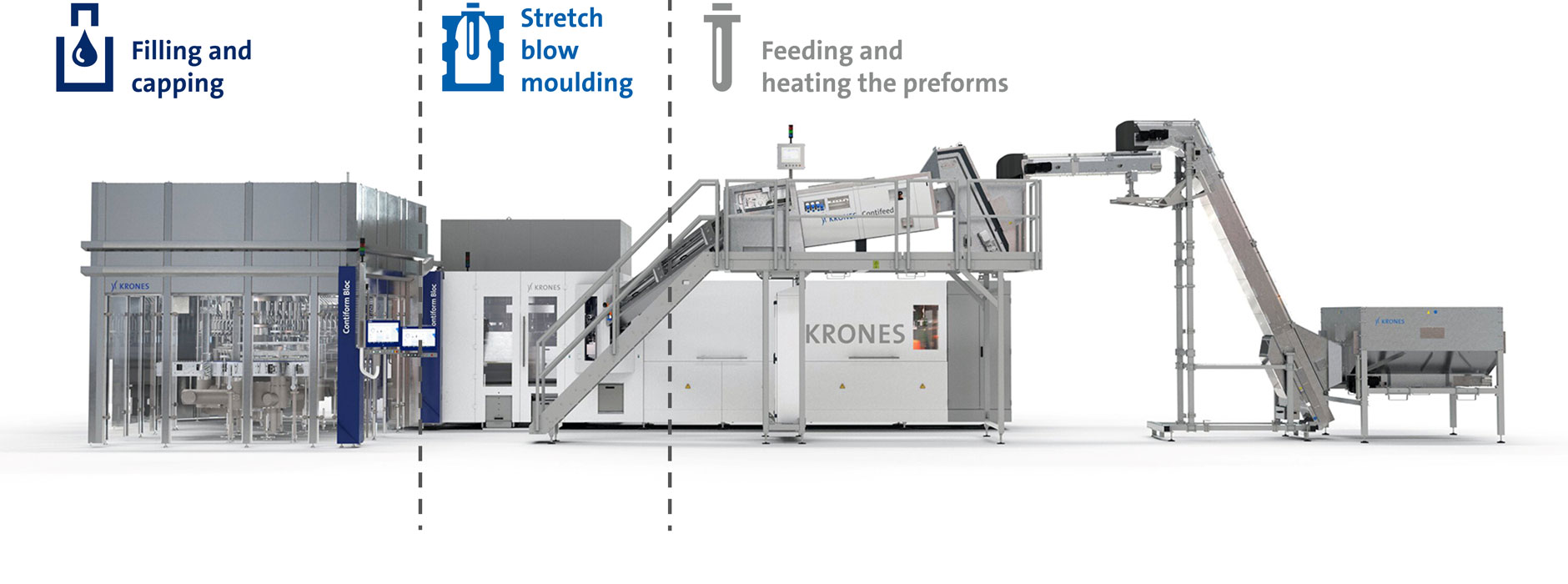
Components
- Torsion-resistant platform with skip-and-run technology
- Only four internal horizontal preform and container transfer points
- Actively controlled transfer grippers
- Five high-precision Monotec servo motors with real-time synchronisation
Infrared heating technology
- Parabolic reflector for top infrared emitter
- Adjustable base reflectors: adjustable to the respective preform length
- Maintenance-free system of ceramic reflectors
Air Wizard Triple
- Further developed compressed air recycling system with intermediate pressure levels for internal re-use of the compressed air
- Automatic self-optimisation of the blowing air recycling process
- Significantly reduced switching time dispersion
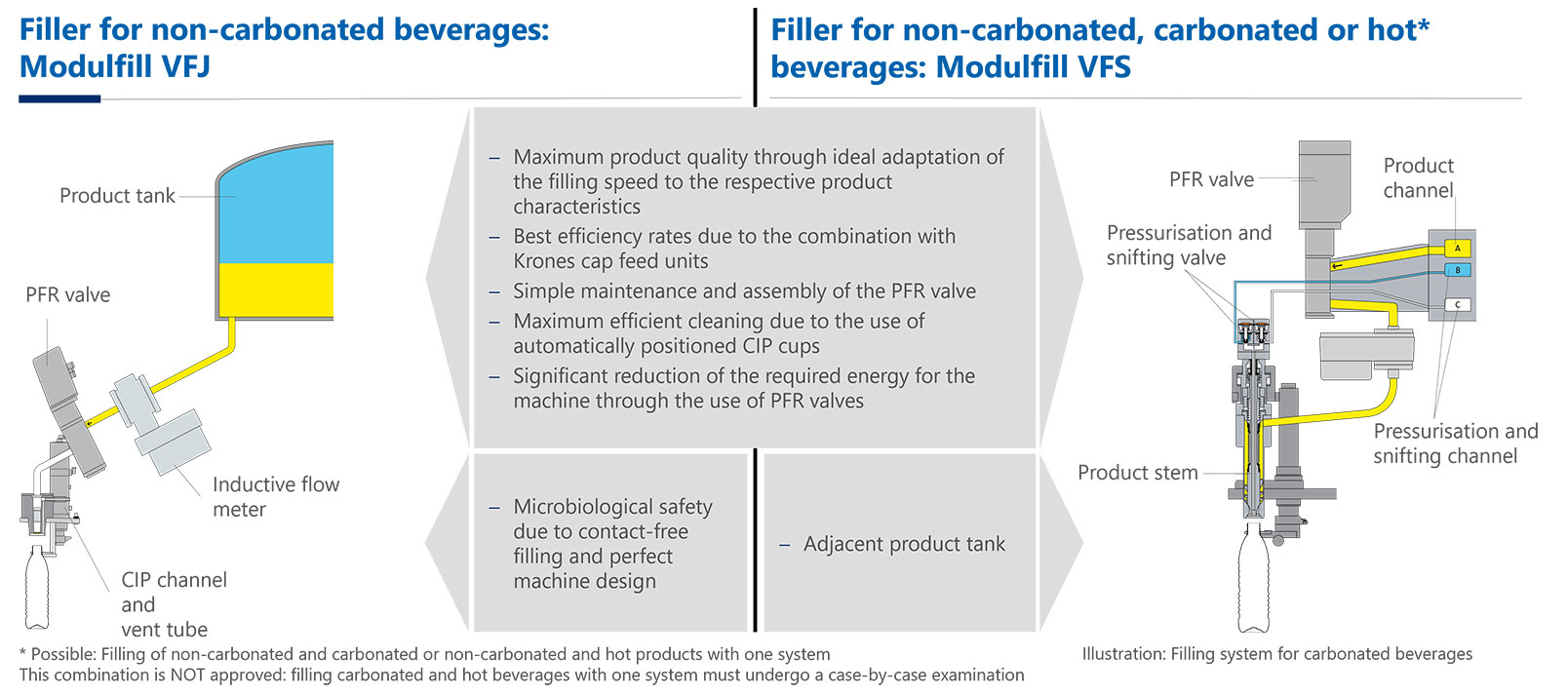
Drive technology
Servo drives use throughout all applications
- Energy-efficient
- Low wear
- Reliable
Transfer technology
- Actively controlled transfer grippers
- Actively controlled transfer grippers
- Quick and very precise preform and bottle transfer
- Smallest possible contact area between the material and the machine
- Gentle conveyance also for light-weight containers
- Reduction of handling parts
- No PET abrasion during the transfer
Servo Joint Control (SJC)
Single machines or block mode? Both is possible: Because with the Servo Joint Control, you can electronically decouple the blow moulder, labeller and filler from the block.
- Automatic decoupling during malfunction
- Automatic synchronisation during restart
- Manual decoupling of individual machines for efficient change-over processes
SJC makes it possible: The Contiform Bloc thinks on its own!
Bottle design and moulds
Creative and in line with the market
At a glance
- Four production centres worldwide with state-of-the-art manufacturing technology
- Container design experts at all four locations
- Design and production of mould types for all Contiform series
- Mould validation on our own technical centre systems
Benefits to you
- Customer-oriented consulting: Creative, functional, unique
- Individual designs with a view to customer requirements and feasibility in the beverage line
- Experience from more than 20,000 moulds per year
Your benefits
In comparison to a conventional line layout
Efficiency on smallest space
The Contiform Bloc requires up to 30 % less space than a blow moulder and filler installed in a conventional single machine arrangement. In addition, the compact line layout reduces potential sources of interference.
Sustainable block concept
The direct combination of individual machines into a block pays off twice: An air conveyor system for the blow-moulded containers, a bottle rinser or conveyor sections are no longer required, which, in turn, results in a reduced consumption of water, compressed air and energy in the complete line.
High hygienic standard
Having only a few interfaces and conveyor sections are key factors in achieving a high degree of cleanliness for the bottle material. The direct transfer of the bottles from the stretch blow moulder to the filler and capper prevents dirt being brought in.
Low operator requirement
The Contiform Bloc offers a good overview, short paths and a standardised operating concept. It also requires little change-over work and has an optimised maintenance program thanks to the use of servo technology.
Efficient and flexible line concept
With the Contiform Bloc, you are optimally prepared for bottle or product change-overs. It allows both, line change-over and restart in a quick and reproducible way.
This is why the Contiform Bloc is enviro-classified
Energy efficiency
- Increased station performance during stretch blow moulding and labelling
- Reduced energy consumption thanks to the omission of transfer starwheels and redundant components
- Height-adjustable base thermal shield and frequency-controlled neck finish cooling system
- Energy-efficient separated vacuum during labelling
Media efficiency
- Efficient cooling of the entire block
- Air Wizard Triple air recovery system
- No compressed-air consumption during the filling process
Environmental compatibility
- Use of enviro-compliant lubricants
- Recoverable CIP media
This product is enviro classified
Top technology for ecologically efficient production

The Krones sustainability programme enviro: top technology for ecologically efficient production.